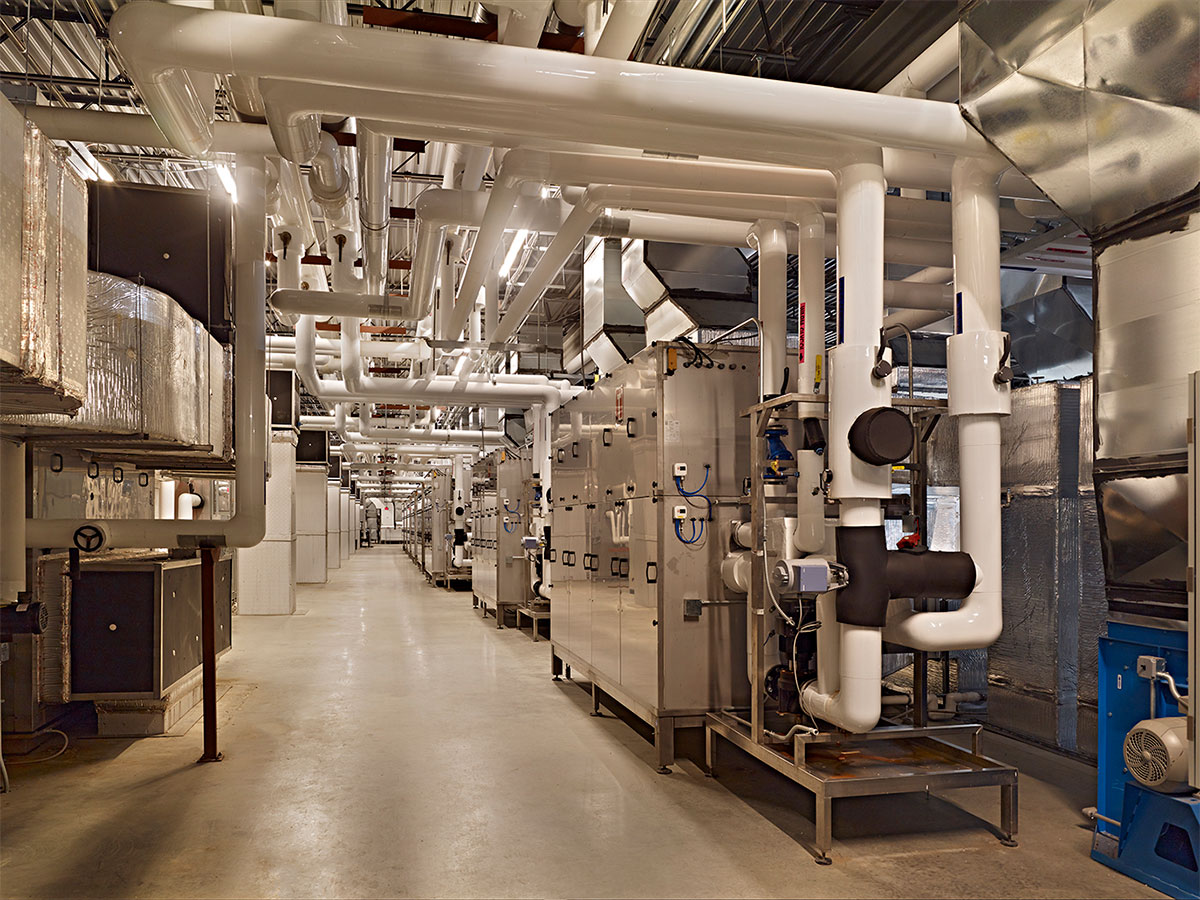
How to Make Energy Codes Work for Your Company
Superstorm Sandy might not rank at the top of the world’s all-time worst natural disasters list, but the post-tropical cyclone was the subject of an interesting study about building envelopes and energy code compliance.
In 2012, millions of New York City buildings were plunged into the darkness without running water for weeks. To assess the danger in six different types of buildings, a study was performed by the American Council for Energy Efficient Economy (ACEEE), and run using historical weather data. All six structures posed serious health risks to inhabitants after one to three days without power or heat. To determine how improvements to the building envelope could improve habitability, the models for each building type were modified to comply with energy codes in effect in NYC from 2010 to 2013, and to a more stringent high-performance building standard.
The results confirmed that a building meeting the requirements of energy code showed substantially improved performance during extended blackouts, while in some cases the “high performance” buildings were so improved that they became merely uncomfortable, rather than dangerous. Envelope advancement and adherence to related regulations also produces well known benefits, such as reduced energy consumption, lowered operating costs and decreased emissions of greenhouse gases and other pollutants.
Commercial building energy codes are adopted by states and cities to mandate minimum requirements for energy-efficient design during the construction phase of new buildings and upgrades to existing buildings, where there is most opportunity to integrate efficiency measures. Codes vary from location to location due to differences in climate.
There are two baseline building energy directives: The International Energy Conservation Code (IECC), created by the International Code Council; and ASHRAE 90.1, a standard developed under the auspices of the American Society of Heating, Refrigerating and Air-Conditioning Engineers. Updates are generated every few years from both organizations. The latest versions are the 2018 IECC and ASHRAE 90.1-2016, respectively.
Building construction and operations accounted for 36% of global final energy use and 40% of energy‐related carbon dioxide (CO2) emissions in 2017, according to the 2018 Global Status Report. Energy efficiency improvements since 2010 have struggled to offset strong growth in energy demand from rising population, floor area and buildings sector activity. However, the IECC has saved U.S. consumers more than $44 billion and avoided 36 million tons of carbon dioxide emissions since its inception. Between 2010 and 2040, the U.S. Department of Energy expects that model building energy codes will save business and home owners up to $126 billion in energy costs.
There are two primary methods to determine energy code compliance. The prescriptive method clearly states what does and does not comply on a component by component basis. The performance method, which looks at the design and allows for tradeoffs between components, is becoming more widely used.
For example, suppose we demonstrate the latter method at a 600,000-square-foot food distribution facility.
Let’s say initial results conclude that this building does not conform to energy code requirements. The first proposed solution involves modifying the building design approach by increasing roof insulation thickness to 10 inches total. While this is the least impactful way to modify the building envelope design to achieve energy code compliance, there may be little to no long-term benefits.
An alternative approach is to change the building skin material to achieve compliance. Evaluation of different building skin material types can lead to potential savings in material costs, increase in work productivity and reduction of lifetime operating costs. This method, isn’t, however, a single solution for all buildings because location, type and building characters all vary. Other building systems may need to be modified/upsized (steel/concrete) to support different skin types, reducing the initial potential savings.
Evaluate. Compare. Decide
No two projects will be the same. Project locations around the country dictate code stipulation based on climate zones and local requirements. Some building skin materials may be required or not allowed by planning/zoning departments. Building use and height play key roles as well. One skin design may be more cost effective for a low-height process facility, while another may work better for a taller, high-pile storage facility. Building skin material type can affect project schedule and sequencing. Non-structural building skin may be more beneficial than load-bearing because it allows multiple trades to work concurrently to seal the building.
With the constant change in energy codes, all building envelope designs should be evaluated to maintain both client expectations and local regulations. It’s important to work with a reputable Design-Build firm to assist in developing design and construction strategies to ensure not only energy code compliance but to maximize energy efficiency and cost savings in your facility.