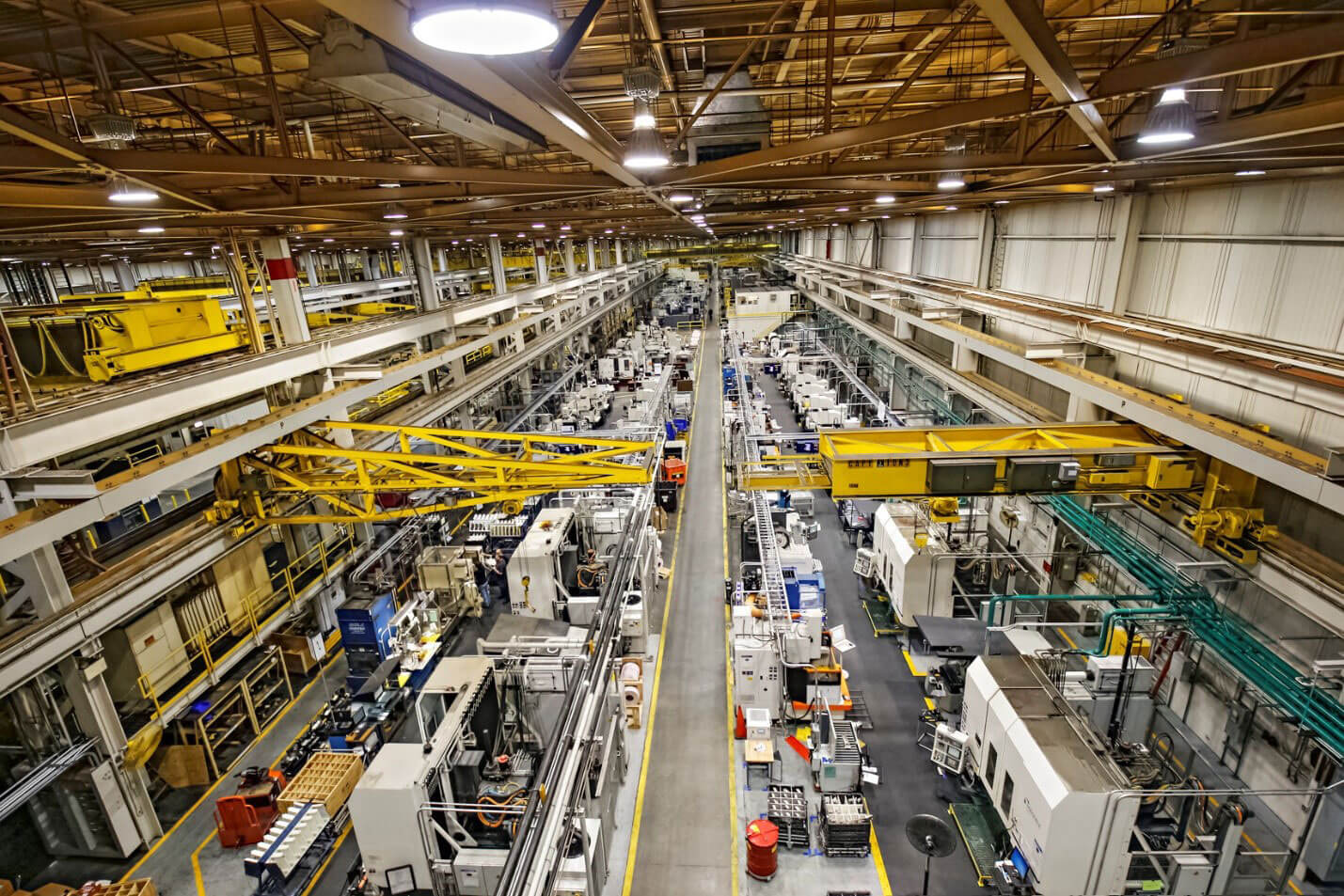
How We Successfully Deliver CapEx Projects in a Fully Functioning Manufacturing Facility
My day begins with a bowl of shredded wheat and two cups of 8 O’Clock Coffee. Black. I run through a mental checklist while I’m driving to work, visualizing what I need to do: proposed activities, subs assigned to my projects and what areas involve the most risk. I consider conduit runs, pipe routing, equipment placement, material staging, man-power distribution, and potential safety hazards. When I arrive, I put on a hard hat, orange reflective safety vest, safety glasses, ear protection, gloves and toed shoes. There’s a lot at stake.
Part of my job revolves around flying a piece of equipment from one location to another. In other words, we are relocating the equipment vertically utilizing overhead cranes. Each crane has a 10-ton (20 thousand pounds) maximum lift capacity. When we set out to move equipment that weighs 20,000 pounds, we must incorporate special rigging (two cranes) in order to accommodate the move. It is imperative that a solid approved rigging plan is in place, each piece of the rigging apparatus is inspected, and all personnel and bystanders are aware of the move.
We cordon off the “fly zone” with red danger tape and advise workers to clear the area while the fly-over is taking place. The cranes lift the equipment and allow it to be carried above the production floor and equipment during relocation. This is dangerous work because if a piece of equipment falls during relocation, people could be seriously injured or killed, not to mention the financial impact of damaging flooring, equipment or parts.
What’s Different about Industrial CapEx Projects?
I manage CapEx projects for large manufacturing companies in South Carolina. By CapEx, I mean capital expenditures that might include any of the following: purchasing property, buildings, equipment or technology; upgrading existing property, buildings, equipment and technology; or building new facilities.
While most large manufacturers have electricians, mechanics and maintenance teams on staff, we are called on to handle more complex projects for clients producing sophisticated industrial parts and materials. They need assistance with project planning, design and execution. Sometimes the planning process highlights which projects are viable and which are not. Our strong client relationships allow us to effectively communicate with all parties involved to perform efficiently in oftentimes hazardous working environments.
We are moving pieces of equipment up to 100,000 pounds in areas with high voltage, high pressure gases and 20-foot holes in the foundation. My team must ensure that the working environment is safe, not only for every single person at the occupied facility, but also the multi-million-dollar parts and equipment. Because every activity has the potential to disrupt production of these expensive parts, each project must be carefully planned and executed, including securing the best subcontractors for the job.
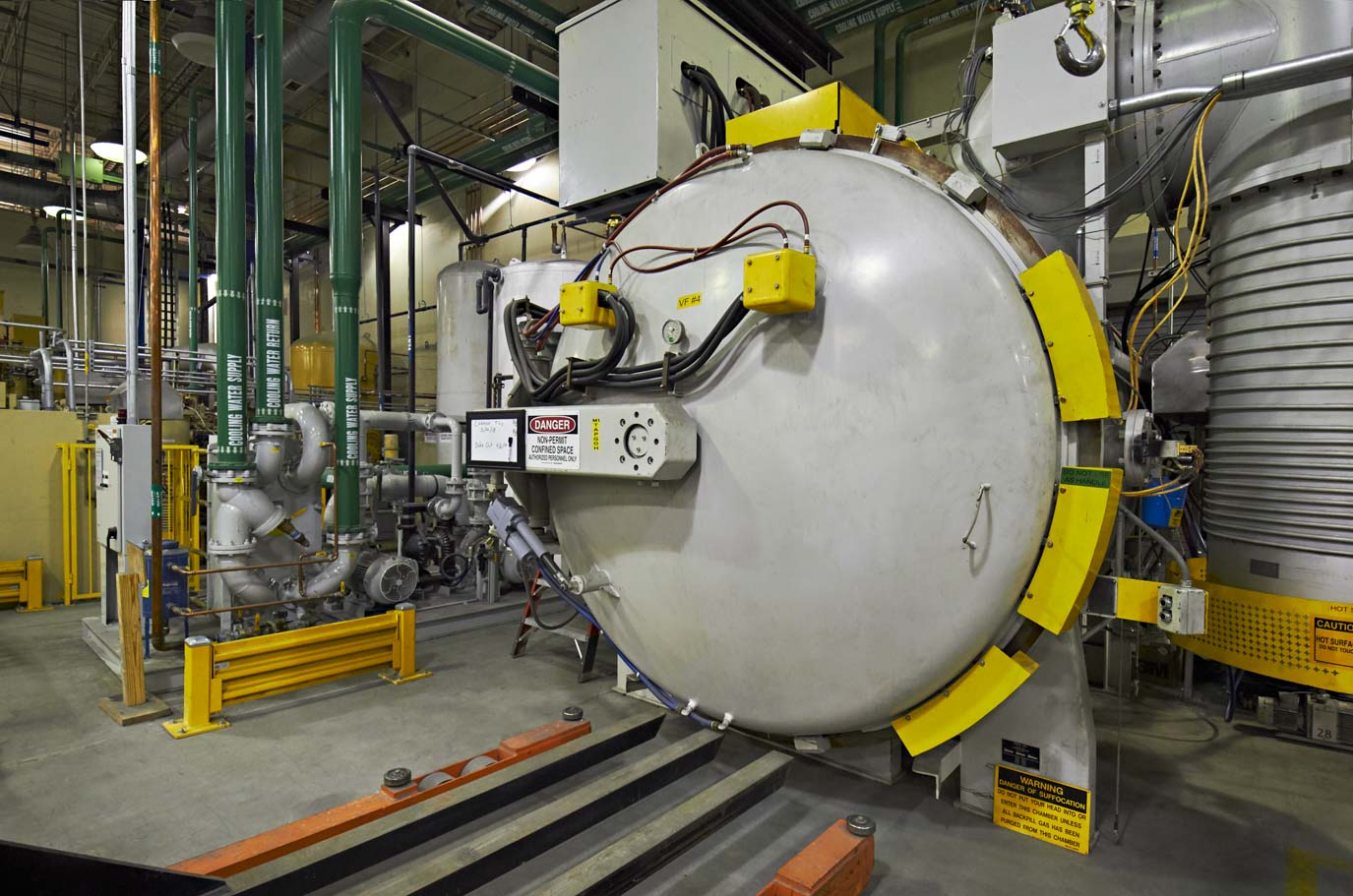
Design-Build Playbook for CapEx
Our challenge then is to develop creative strategies in our Design-Build playbook for limiting production downtime while remaining vigilant about safety. This is how we do it:
- Schedule project work during nights, weekends and holidays. It might be as simple as scheduling a panel tie-in during lunch breaks or overnight. For example, last year for seven days during Christmas break we relocated 65 pieces of Volkswagen-sized machinery for one of a client’s lean manufacturing lines. If we hadn’t worked during this holiday, the project would have taken at least a month. In addition, by conducting work during Christmas break, A M King limited risk exposure by working in an unoccupied area of the plant.
- Stagger work so that it’s the least invasive to a particular area or cell. A recent project involved a problem with a 3D printing machine that was producing defective parts. Investigation revealed the temperature, humidity and dew points in the room did not match machine specifications and we were tasked with correcting the problem. We examined the building shell seal and heat loads from existing equipment and put those calculations into sizing and installing an HVAC unit. Working on half of the room for two weeks and then moving to the other half of the room for two weeks made this project particularly efficient, reducing production downtime.
- Coordinate with production and maintenance teams. Suppose you’ve got filters on a machine that need to be changed. We coordinate with client teams to schedule our work in that area while the machine is being serviced, taking advantage of the time that the equipment will already be down for regularly scheduled maintenance.
- Set up temporary stations while working on a permanent solution. There are times that production trumps construction. Temporary work areas supplement production needs during construction and might involve installation of a single piece of equipment or an entire production cell. For example, we set up interim grinding stations while we were working on permanent solutions, ultimately saving the client 10 percent of the client’s cost.
- Utilize prefabrication. A M King maximizes use of prefabrication in industrial manufacturing projects to minimize impact on facility operations, provide overall project cost savings, reduce project schedules all while providing a safer working environment.
- Be flexible during construction. Despite extensive planning and schedules, issues arise that demand immediate solutions and perhaps deviations from the original plan. The field staff can play a vital role in providing safe, effective, cost-saving solutions while the project is progressing.
What’s the bottom line? We’re not shutting down an office where employees can take their laptops to a different area. We’re working around manufacturing lines with multi-million-dollar equipment running 24/7 and producing highly specialized, big-ticket product. Our mission on every job is to consistently, safely and efficiently manage complex projects for our clients so that they can focus on production and growth. Every day I leave work satisfied that my team did what we said we would do and it was done safely, quickly and well.