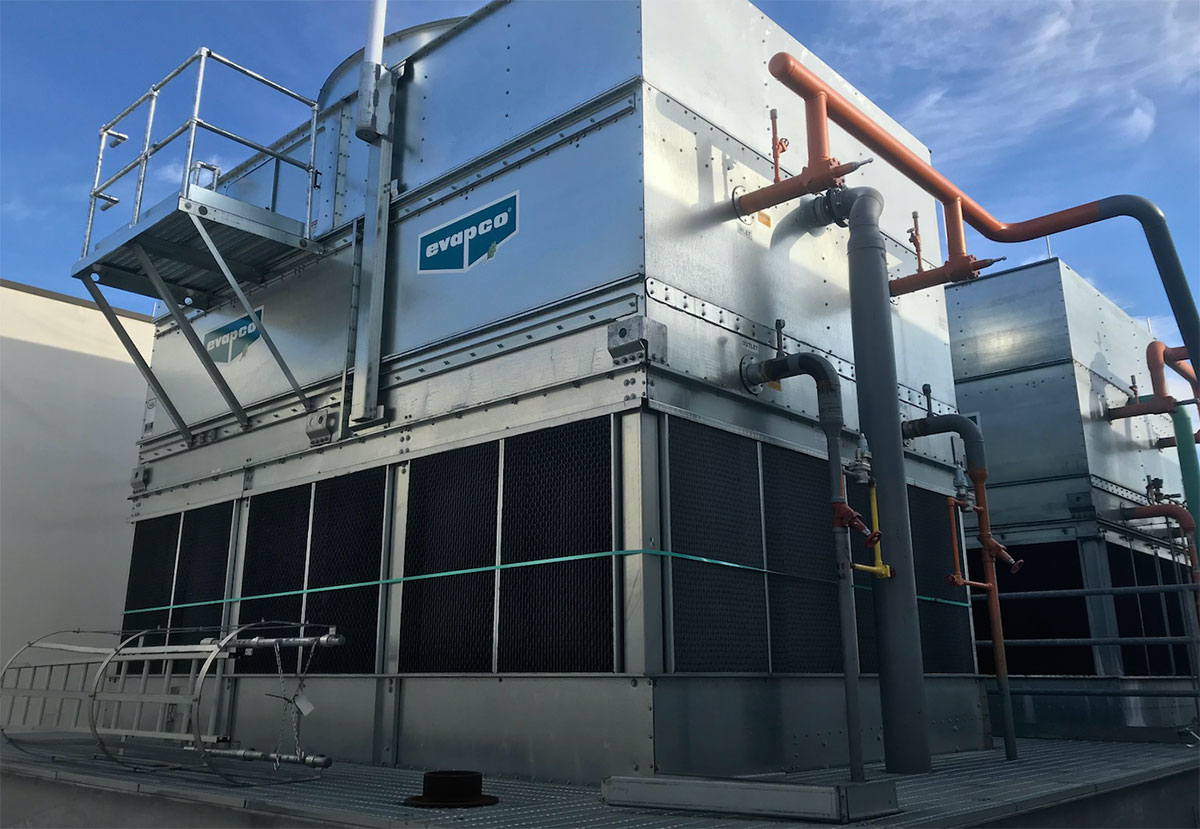
Electrical Design Plays a Critical Role in Facility Expansions/Renovations
My time as an electrical design engineer in this industry has shown me the absolute necessity to design with intent, foresight and flexibility. Those strategies are more important than ever as we find ourselves riding a wave of desire for renovations/expansions versus Greenfield projects. Last month, Food Engineering magazine analyzed the ratio of expansion/renovations to new projects from 2006 to 2017. During the past six years, the ratio has increased and in 2017, three out of four projects reported were expansion or renovations.
The challenge for Design-Build firms is often working with significant limitations during an expansion or renovation that demand a team approach to problem solving. I am fortunate to work with a group that sees such situations as an opportunity and a promise to the client to bring creative thinking and originality to the job. We can’t use the same cookie-cutter methodology, even when presented with seemingly similar obstacles. Take a look at these three examples that show how we solved a comparable predicament three different ways.
The challenge for Design-Build firms is often working with significant limitations during an expansion or renovation that demand a team approach to problem solving. I am fortunate to work with a group that sees such situations as an opportunity and a promise to the client to bring creative thinking and originality to the job. We can’t use the same cookie-cutter methodology, even when presented with seemingly similar obstacles. Take a look at these three examples that show how we solved a comparable predicament three different ways.
The Heartbeat of Perishable Space
Our large, food distributor client needed to expand its perishable footprint by 60 percent at three different facilities. The projects consisted of similar expansions, one right after the other. In each case, a significant driving force was the need for 100 percent emergency generator backup to maintain 24/7 operations.
Case #1: Design with constraints of existing conditions in mind.
The first facility in the series of expansion projects was 100,000 sf, which was to be expanded to 148,000 sf. Given the size requirements, the existing electrical equipment would not provide the necessary backup capabilities to support the full load of the expansion. Therefore, a replacement or supplemental emergency generator was needed. In addition, we had the added challenge of working in a restricted space to accommodate coordination with the local airport authority and to protect forested conservation areas located adjacent to the property.
As with any client, we took a look at our options and engaged our engineers and contractors early in the process. We came up with a better solution utilizing an exterior supplemental generator in conjunction with the existing interior generator and paralleling gear that allowed the generators to talk and share the load. In this case, the paralleling gear was “on board” versus a large switchgear (simply, we split the equipment in several smaller pieces, which included new paralleling circuitry mounted on each generator; a new distribution board to integrate new and existing power wiring; a new control panel on the new generator and replacement of the existing control panel on existing generator.) This meant that the equipment was sized for proper load requirements and consumed less space.
Case #2: Plan and design to meet schedule requirements.
The second facility in the series, which was to be expanded by 55,000 sf, had the same emergency generator configuration and overloading issue as the first facility. Our preliminary schedule for the Perishable expansion from groundbreaking to turnover was seven months but the equipment lead-time for the paralleling switchgear in this case, versus “on board,” would have been eight months. A month with no emergency generator backup was unacceptable, so we came up with an alternative solution utilizing two generators working independently of each other. Although not preferred in most scenarios, the new electrical design didn’t require use of paralleling switchgear, thus removing the potential for extended lead-time and keeping to the owner’s schedule.
Case #3: Design the facility to be as cost-effective as possible.
Even though this third building was similar to the other two, it was not identical and we had to find a new way to answer the challenge of providing more strength to the emergency generator system. Like the first two cases, it was decided that providing a supplemental generator was the best approach. Unlike Case #1, we did have clearance and the option of moving doors around to accommodate the large paralleling switchgear. In addition, unlike Case #2, we were able to procure this this equipment within the allotted schedule. However, regarding the generator itself, it would have been easy to procure another generator from the same vendor, but after researching the issue, we decided to go with a more economical option that would also work in tandem with the existing generator. We accomplished both goals.
Conclusion: Taking a one-size-fits-all approach is dangerous. Even if similar problems arise in separate facilities for the same client, it is important to focus on the unique issues in each building; be mindful of preexisting conditions, schedule and cost; and work together as a team from project inception to create innovative solutions for the client.
Tim Gause is an Electrical Design Engineer whose clients include Northeast Foods Inc., SK Food Group, ALDI Inc., and Henry Avocado Corporation.
If you’re considering expanding or renovating a cold storage facility, contact one of our experts at [email protected] or read this related resource: