
Pandemic Pushes Food Industry to Amplify Automation
Nearly three years ago, the owners of Daniele, Inc. took their 73-year-old family food business in Rhode Island from artisan producer of specialty cured meats to robotics big shot. The company’s new salami processing area — designed and built by A M King — is comprised of both magnetic and laser-guided robots for material transfer. The renovated and expanded facility provided Daniele with the ability to double the production of salami, while retaining its Italian heritage and craftsmanship. Automation also reduced manpower there by 70 percent.
It was tough enough to find skilled labor at that time. Fast forward three years and we are in the middle of a pandemic. Food processors and distributors are not only concerned about finding qualified employees, but they must also worry about keeping workers healthy. Consumer spending is shifting and land for new development is becoming scarcer. Above all, technology marches on, not just a playground for innovators anymore, but rather a necessity to stay competitive during these troubled times.
Is Implementing Automation the Answer?
Every day I see the intense pressure that food processors and distributors are under to continue operations, despite restrictions and new obstacles brought about by COVID-19. Many food industry operators are recognizing that they will have to modernize to keep pace with the competition and that may mean implementation of automation. Because they are part of an essential industry, many are becoming more open-minded and experimental. They want to know what their return on investment would be for new technologies. Are systems smarter, more intuitive and less expensive? Is implementing automation in their facilities the answer?
According to a new market research report by Meticulous Research, titled, “Food Automation Market by Component, Mode of Automation, Application, and End-use – Global Forecast to 2027,” the food automation market is expected to grow at a Compound Annual Growth Rate (CAGR) of 9.5 percent over the next seven years– from $15.5 billion in 2020 to reach $29.4 billion by 2027.
Not all food operators are jumping on the bandwagon yet, however, perhaps due to the perceived or required investment, or maybe, in some cases, lack of knowledge. Automation can be an amorphous term for food companies that may not have utilized it thus far. When I talk about it with clients and prospective clients, we most often focus on Automated Storage & Retrieval Systems (ASRS) and robotics.
While each company’s individual response to automation will be different, the factors that are driving companies to at least begin moving in that direction are universal: shift in consumer spending this year; operational challenges and cost pressures; lack of available, affordable and good quality land; and increasing technology advancements and accessibility. Let’s explore how each of these influences is moving the automation ball forward in food companies.
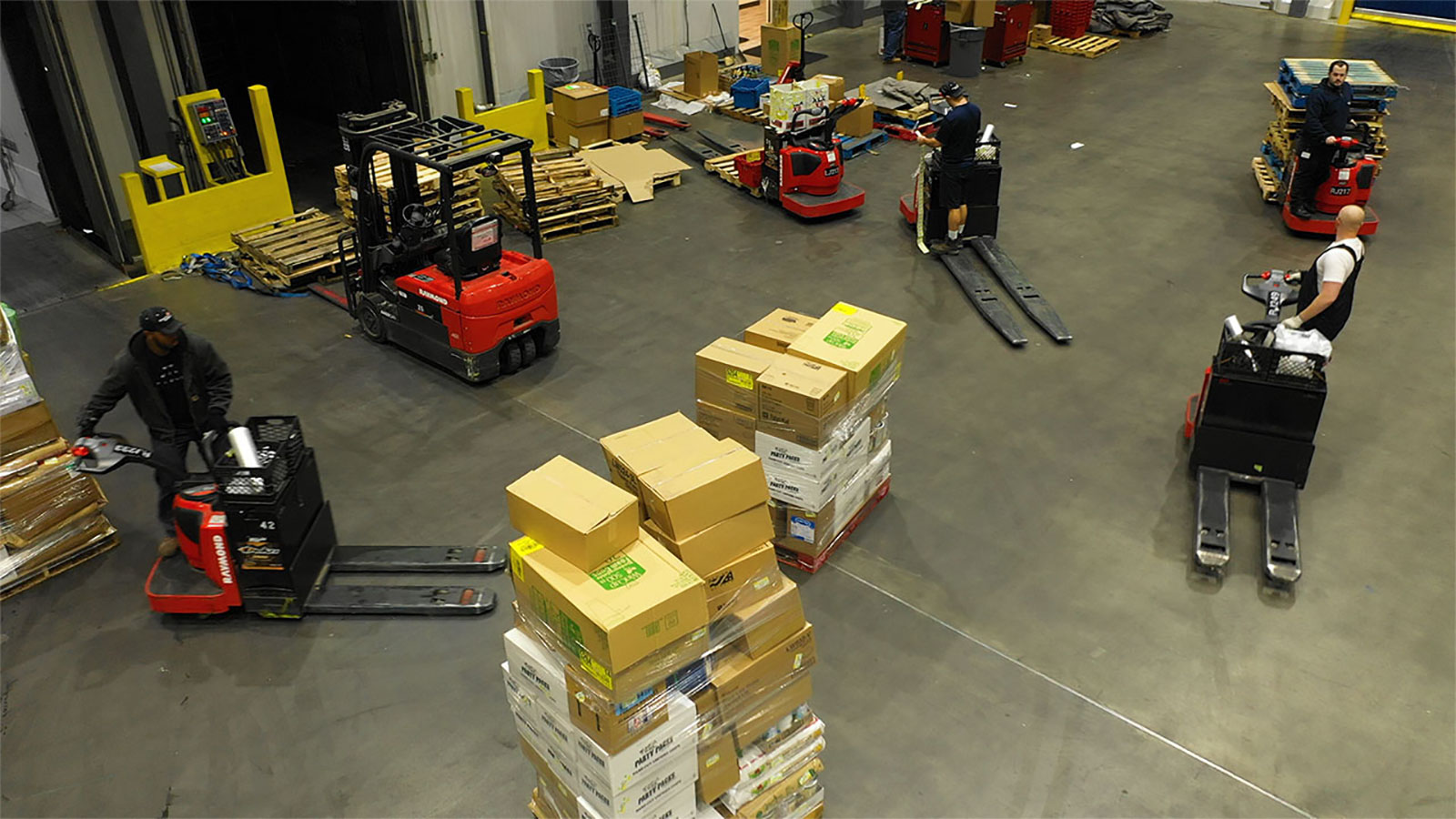
Shift in Consumer Spending Patterns
The retreat to home kitchens has led consumers to spend more at grocery stores and online. This in turn creates need for more efficient systems to requests for quick, convenient and safely prepared, packaged and distributed foods. Higher quantities and different types of food—including immunity boosting food products and comfort foods—need to be produced in a shorter amount of time. How can food companies implement alternative strategies to tackle skyrocketing consumer demand?
Online grocery sales tripled in the early part of the COVID-19 pandemic as food retailers ramped up an already growing e-commerce business, according to FMI’s Food Retailing Industry Speaks 2020 Report. To meet the demand crush, 83 percent of retailers surveyed said they added more staff to handle online fulfillment, and 37 percent earmarked more workers to handle delivery of online orders.
FMI noted that, with shelter-in-place and stricter social distancing guidance in effect early in the pandemic, more than half of retailers (51%) urged customers to order online. Eighty-three percent also reported they are exploring new technologies to improve the customer experience, versus 72 percent last year, and 81 percent aim to leverage technology to sharpen efficiency, up from 75% in 2019.
Aim is the operative word here. Many companies I communicate with have not implemented big changes yet, but you can bet they’re thinking about it and asking questions. When you’re moving perishable product from freezers to trucks–whether it’s pallets of ice cream, pizza or crispy chicken strips– it’s always a race against the clock. But when a confluence of factors drills the minutes that you had down to mere seconds, how can you sustain this effort? Some of these companies are figuring out how to begin accommodating automation to address online consumer needs.
Operational Challenges and Cost Pressures
It’s worth remembering that most growing businesses in the U.S. are not putting money into people, but rather investing in equipment and processes; and that isn’t as negative as it sounds. The aforementioned Daniele Inc. is a case in point. As warehouse worker safety is currently top of mind this year, warehouse automation could be the key to food processors meeting food safety standards without a hands-on, human-focused approach. These companies are realizing that they must rely less on their labor force.
Consider another A M King client, the owner of a fully automated baking facility in North Carolina that only employed a handful of people when COVID-19 hit. While in a relatively great position, they continue to look for means to improve efficiency. To use another example, a national grocer that is not utilizing very much automation can’t hire enough people to meet the demand. Further, they are experiencing pressure to keep employees safe after they come on board.
Food processors have similar, but amplified, concerns about production line staff that has historically worked shoulder to shoulder. In California, a single food processing plant had 153 positive cases of COVID-19 earlier in the year. In each of these three cases there are different levels of impact and urgency related to labor issues; however, all desire more automation. Ultimately, food operators are looking for increased productivity and to get there, may have to step outside their comfort zone.
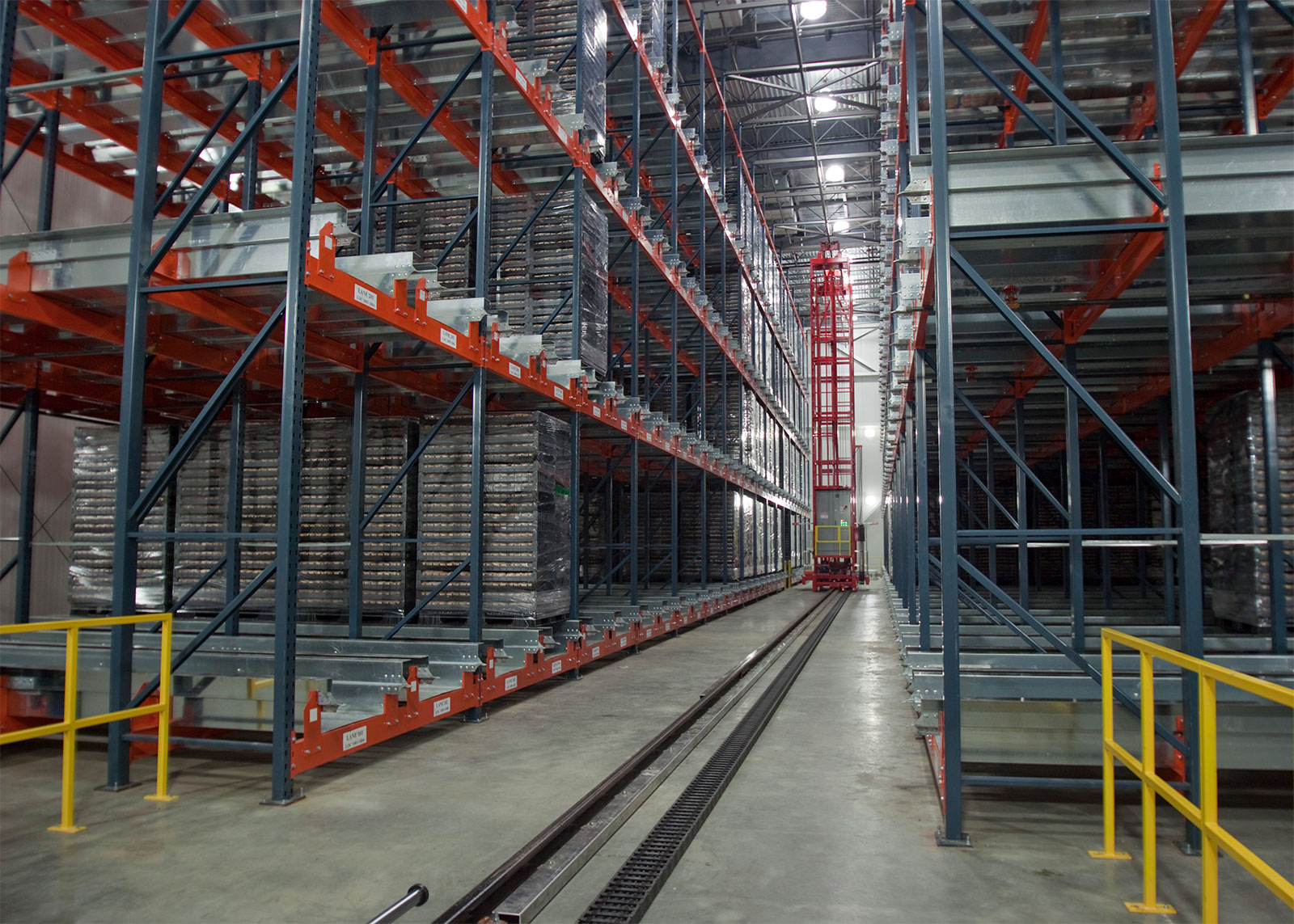
Lack of Available, Affordable and Good Quality Land
One of our distribution clients was considering an Atlantic coastal city to build a new facility. We discovered that the populated area was 10 times more expensive than tracts further inland. Another food distribution client that needed to be closer to its customer base chose an urban site in the Northeast part of the country that isn’t large enough to build wide. They will have to go tall instead, and when you go tall, it is critical that you install automation.
Another client, Northeast Foods, Inc., producer of breads and buns for more than 50 years, commissioned A M King to significantly increase freezer capacity and efficiency at its Automatic Rolls facility in Dayville, CT. The expansion contains accommodations for a cutting-edge ASRS System in the freezer, which features fully automated racking storage up to 40 feet at -20-degrees. The system reduced human interaction, helped regulate temperature in the freezer and decreased the need for lighting in the area.
Increasing Technology Advancements and Accessibility
The increased reliability and number of technology options are driving companies to consider automation. With improvements in robotics technology, such as grippers, collaborative robots (which can accurately and uniformly pick and pack products, even fragile produce), and mobile robots, we will likely see many more applications going forward. The task for distributors will be identifying and developing automation that can handle 1000+ different types of products, but it will happen.
Food companies have been assessing their operations this year. New ideas have been brought to forefront. Now it’s time for action. Our design group has already started implementing ideas that have been talked about in 2020—ranging from building new facilities specially designed to be fully automated or reconfiguring existing facilities to incorporate new technology. In 2021 and beyond we will be challenged to help our clients with their specialized needs, and they will, without a doubt and for unique reasons, be adopting some level of automation.